cast iron
Custom castings
We develop and produce cast iron for different applications. Whether it concerns an end product or a semi-finished product: SN Cast Iron makes it. Our customers are mostly in the industrial sector. We often make products such as engine housings, machine parts, or similar windmill axles. You ask, we pour.
Custom castings
We are the ideal partner for customization. Whether it is a completely new product to be developed or a cast piece for which you already have a drawing. Because of our experience, we always know how to achieve the best result. Of course we discuss with you what kind of cast iron is most suitable for the product you have in mind. With the choice of lamellar, ductile or ADI cast iron, we can help you. For industrial applications, nodular cast iron is usually used because of the good mechanical properties. it has a high wear resistance and compressive strength. Ideal for among other things loading and moving parts.
Advantages of cast iron
Cast iron is a molded alloy of iron, carbon manganese and silicon. It is made through melting rough iron with cokes and lime in a dome, induction or drum oven. Then the liquid iron is poured into form (often of molding sand). The advantage of cast iron compared to cast steel is that cast iron can be poured better and it is more fluid than cast steel by high temperatures. This makes it easier to achieve a smoother end product also post-processing is necessary to a lesser extent
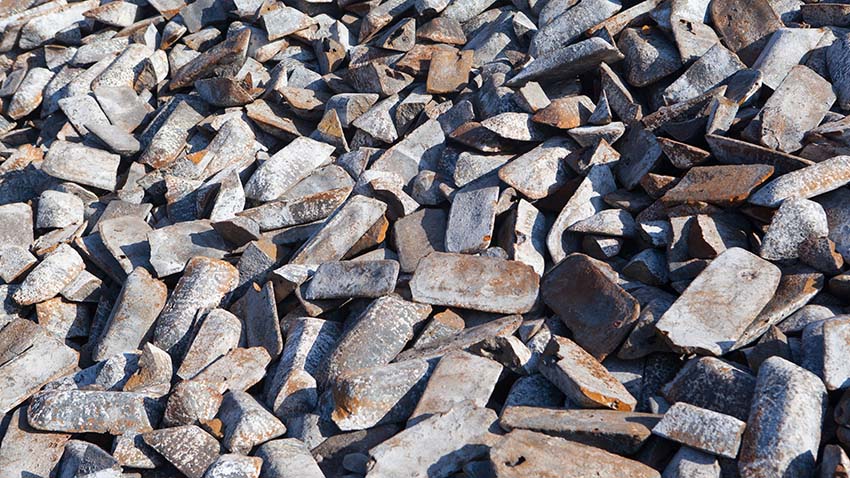
Experienced ironfounder
If you choose for SN Cast Iron, you choose experienced iron founders with a passion for their profession. Owner Stef Nas has more than 30 years’ experience in the development and production of cast iron products.
Every link within SN Cast Iron is aware that passion goes hand in hand with quality. In this way every individual within SN Cast Iron develops every day as a team as strong as iron.
Experienced iron founder
If you choose SN Cast Iron, you choose experienced iron casters with a passion for their profession. Owner Stef Nas has more than 30 years of experience in developing and producing cast iron products. Every link within SN Cast Iron is aware that passion goes hand in hand with quality. In this way, every individual within SN Cast Iron develops every day. The team is therefore as strong as iron.